Synthesis and Characterization of Stainless Steel Foam Via Powder Metallurgy Taking Acicular Urea As Space Holder
Shailendra Joshi1, Gaurav Kumar Gupta2, Mohit Sharma3,Amit Telang4, Taru Mahra5
1,5Department of Mechanical Engineering, SIT, Pithoragarh, Uttarakhand
2Materials Science and Engineering Department, CSIR-AMPRI, Bhopal (M.P.)
3Department of Mechanical Engineering,NIT, Kurukshetra, Haryana
4Department of Mechanical Engineering, MANIT, Bhopal
DOI : http://dx.doi.org/10.13005/msri/120108
Article Publishing History
Article Received on : 09 Jun 2015;
Article Accepted on : 23 Jun 2015
Article Published : 24 Jun 2015
Plagiarism Check: Yes
Article Metrics
ABSTRACT:
Stainless steel foams are produced via powder metallurgy process taking acicular urea as space holder contributing porosity with 40-70 volume %. The resulting changes in microstructure of compact after each operation comprising cold compaction, pre-heating and sintering are discussed along with causes with the help of SEM micrograph. The processed foam samples using 40 % urea by volume are quite regular and acicular in shape but with increase in porosity regularity starts diminishing. It is observed that the foam samples with 40 % porosity doesn’t show any plateau stress as in aluminum foams but those with 50 % porosity (approximately 80 MPa maximum plateau stress) and 60 % porosity (approx.45MPa) shows plateau region in true stress-strain diagram during compression test due before final densification process. It is observed that with increasing porosity plateau stress decreases, since lesser force is required to densify the foam. Therefore the stainless steel foams with low porosity can be used in light weight high strength applications e.g. structures whereas with high porosity have impact energy absorbing applications e.g. damping elements in buildings or vehicles, etc.
KEYWORDS:
Acicular; Plateau stress; Porosity; Powder metallurgy; Stainless steel foams
Copy the following to cite this article:
Joshi S, Gupta G. K, Sharma M, Telang A, Mahra T. Synthesis and Characterization of Stainless Steel Foam Via Powder Metallurgy Taking Acicular Urea As Space Holder. Mat.Sci.Res.India;12(1)
|
Copy the following to cite this URL:
Joshi S, Gupta G. K, Sharma M, Telang A, Mahra T. Synthesis and Characterization of Stainless Steel Foam Via Powder Metallurgy Taking Acicular Urea As Space Holder. Mat.Sci.Res.India;12(1). Available from: http://www.materialsciencejournal.org/?
|
Introduction
In modern era, metal foams have emerged as a new class of cellular material consisting of a metal phase containing dispersion of pores. & has become an interesting area for researchers since they possess unique combination of engineering properties such as high stiffness, low density, better impact resistance, high energy absorption potential during compressive deformation, better erosion resistance & ease in giving complex shape [1-3]. Ashby et al (2000) reported that metal foams exhibits high stiffness to weight & strength to weight ratio, thus providing weight savings & cost reduction too. The potential applications of metal foams were provided as a function of their porosity by Banhart. They possess wide range of applications such as low weight sandwich panels, energy absorbing equipment, packing material, structural constituent in air and spacecraft [3-6], biomedical prosthesis [1-3], automotive, ship building & process control domains. Metal foams can be used as bumpers e.g. for suburban railcars, trams or cars as they are excellent energy absorbers due to their special deformation mechanism, the formation of deformation bands [5]. Metal foams display a characteristic compressive stress-strain curve which can be divided to three stages. During small strains (<1-2%) metal foam deforms elastically; than a plateau of deformation (up to 60-80% strain), where the stress is almost constant. Finally, as the deformation reaches the densification strain, thereafter the densified foam deform plastically [5]. Since long plateau region is found at constant compressive stress, foams are suitable for absorbing energy. Most metal foams comprises of aluminium, nickel, magnesium, lead, copper, titanium, steel and even gold as matrix [33].
A group of heat resistant and corrosion steels containing atleast 10.5% chromium. Stainless steel foams are metallic materials with various physical and chemical properties that can be used for several purposes. These foams exhibits high energy absorption, wide range of strength to elastic modulus ratios & huge ductility [7, 8]. The stainless steel foams have their main applications as sandwich panels, structural elements & beam cores where low weight and large specific rigidity is needed [32]. Steel foams are favourable materials for crash protection, building ships and packaging. The high energy-absorption properties of stainless steel foams & their lower cost makes them prospective competitors. They can be used in heat exchangers in the form of foam covered tubes and also as deflector plate for thermal and acoustic applications [7,8].
In general, two processes have been invariably used for metal foaming: (1) the liquid metal route where foaming is accomplished by direct foaming of melt with gas or some foaming agent [2, 9–12] and (2) the powder metallurgy route where foaming is affected by foaming a sintered compact [2]. Other routes include sintering of hollow spheres [13] and pressing the material around a filler followed by sintering with subsequent filler dissolution or decomposition [14–16, 17, 18]. Recently, experiments have been carried out in microgravity conditions to see its effect on the stability of foams and obtaining highly porous structures [19–22].
In 1943, the first metal foam was invented, by Benjamin Sosnick at San Francisco California. Metal foams were first produced through powder metallurgy at the Fraunhofer Institute in Bremen (Germany) [ref]. Fraunhofer IFAM & Fraunhofer USA Centre-Delware had conducted further development & application of metal foam technology [23, 24]. PM based process known as space holder method can be used to manufacture foamed metals. The space holder method starts with blending of metal powders along a suitable space holder material, after that hydraulic compaction of mixture (e.g. uniaxial pressing) is done that produces metal powder-space holder mixture compact referred as green compact. The green compact is then heat treated at a relatively low temperature to release the space holder, resulting in an unfired cellular foam metal structure. Finally, the compact is sintered at relatively high temperatures to provide structural integrity. This method permits a direct manufacturing of required shape foamed components having comparatively uniform cellular structure and a high level of porosity (60-80%). In powder metallurgy, space holder techniques are usual and offers a broad extent of structure and properties. There are number of methods of eliminating space holders e.g. by leaching , shaking, or by pyrolysis. Various space-holder materials are used such as carbamide (urea), NaCl particle [25-29].
The compression and behaviors of metal foams have been widely investigated in the recent years. Wang et al.[30] also investigated the effects of cell sizes on the compressive strength and energy absorption. Nieh et al.[31] studied the effects of cell morphology on the compressive properties of foams. For characterizing the energy absorption behaviour of stainless steel foams the compressive properties, like the plateau stress and the densification strain must be determined as a function of the properties of the foam. Different from the solid materials, compressive deformation mode of the cell structured materials changes from uniform plastic deformation to localization.
The purpose of our research paper are: synthesis of stainless steel foam through PM route, compression testing of stainless steel foam to find the plateau stress using stress-strain diagram, & to experimentally characterize green compact, pre-sintered stainless steel foam & sintered stainless steel foams by scanning electron microscope.
Experimental Procedure
Stainless steel powder (Type 316-L45, density 7.85g/cm3) and urea particles (average size-2mm, density 1.32g/cm3) are used as the starting material. Stainless steel powder and urea are weighted on electronic weighing machine in a required weight proportion. To prepare the first samples of acicular urea particle 90 %( 22.5 gram) of Stainless steel powder is mixed with 10 % (2.5 gram) of urea particles to obtain the porosity in the range of 40%. After weighing in the electronic weighing machine, powders are put in the crucible and mixed manually for about 15 minutes. The second sample 84 % (21 gram) of stainless steel powder is mixed with the 16% (4 gram) of urea particles to find the porosity of the range 50 volume pct. To prepare third sample 80 % (20 gram) of stainless steel powder are mixed with the 20% (5 gram) of urea particles to obtain the porosity of the range 60%.
The mixture is than compacted in a cylindrical die of 10 mm diameter at a pressure of 250 MPa. The die is placed in the hydraulic compacting machine and is compacted for a time period of 30 seconds. This method produces cylindrical shaped green compact. Preheating of the precursor is done in a tubular furnace at the temperature 3500C, for a time period of two and half hour.
In the sintering process the foam samples are heated up to 11000C for a time period of 110 minute at a heating rate of 10 /min 0C. Then the samples are kept in the horizontal high temperature vacuum furnace for a time period of 60 min., so that whole parts of the samples are attend a constant temperature of 1100 °C. Then the samples are cooled in the furnace. Then the samples are kept in the furnace for a time period of 60 min., so that whole parts of the samples are attend a constant temperature of 1100 °C. Then the samples are cooled in the furnace.
The microstructure characterization is carried out on a JEOL 5600 Scanning Electron Microscope. The stainless steel foams mechanical properties are determined by executing compression test on the sample. At the strain rate of 10-3 s-1, the compression test is performed on Instron universal testing machine.
Result and Discussion
During cold compaction, green compacts measurements are taken with the help of the vernier caliper and weighed by the electronic weighing machine. The theoretical density of the powder mixture is calculated using the mixture rule formula.
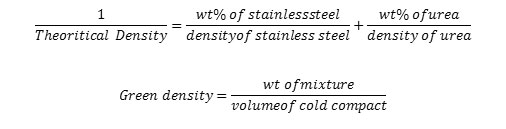
Table1: showing various measurement data of stainless steel green compacts mixed with acicular urea particles
Sample no.
|
SS
(wt %)
|
Urea (wt %)
|
Weight of mixture
(gm)
|
Volume of cold compact
(cm3)
|
Green Density
(gm/ cm3)
|
Theoretical
Density
(gm/ cm3)
|
Green density (%Theoretical
Density)
|
1
|
90
|
10
|
4.19
|
1.045
|
4.000
|
5.251
|
76.17
|
2
|
90
|
10
|
4.64
|
1.121
|
4.139
|
5.251
|
78.82
|
3
|
90
|
10
|
4.72
|
1.125
|
4.195
|
5.251
|
79.88
|
4
|
84
|
16
|
3.717
|
1.062
|
3.500
|
4.381
|
79.88
|
5
|
84
|
16
|
3.182
|
0.946
|
3.360
|
4.381
|
76.69
|
6
|
84
|
16
|
4.123
|
1.099
|
3.750
|
4.381
|
85.59
|
7
|
80
|
20
|
3.44
|
0.939
|
3.660
|
3.946
|
92.75
|
8
|
80
|
20
|
3.93
|
1.032
|
3.800
|
3.946
|
96.30
|
9
|
80
|
20
|
3.54
|
0.991
|
3.570
|
3.946
|
90.47
|
The green compact is observed on the compacted surface using FE-SEM. The micrograph shows the dispersal of urea particles in the stainless steel matrix. In the image the black regions are the stainless steel particles while the white regions are the urea particles embedded in the matrix.
Figure1: showing SEM image of acicular urea particle embedded in the stainless steel matrix
During preheating, the green compact is placed in the furnace on the ceramic plate. After the temperature reached 370 ºC, the green compacts are soaked for 2.5 hrs and then cooled in the furnace. Due to the evaporation of the urea, from the compacted part, pores are obtained. The pores obtained are larger than that of urea particles used due to strain produced by heating and evaporation. The microstructure shows the distribution of pores in the stainless steel matrix. Microstructure shows after the removal of urea in the form of gas as accicular pores. Such pores are formed due to low pressure used during the compaction of the powder mixture & shape of urea particles is also a key factor. Pore size is larger than that of the size of the urea particles because urea particles evaporate after breaking the bonds with the stainless steel matrix resulting larger size voids.
Table2: showing various measurement data of stainless steel pre-heated compacts mixed with acicular urea particles
Sample no
|
Initial wt.(gm)
|
Final wt.(gm)
|
Volume of preheated compact(cm3)
|
Density of preheated compact(gm/cm3)
|
% Density
|
% porosity
|
1
|
4.19
|
3.66
|
0.797
|
4.59
|
58.50
|
41.5
|
2
|
4.64
|
4.13
|
0.890
|
4.66
|
59.44
|
40.5
|
3
|
4.72
|
4.30
|
0.912
|
4.71
|
60.10
|
39.9
|
4
|
3.71
|
2.77
|
0.723
|
3.83
|
48.80
|
51.2
|
5
|
3.18
|
2.43
|
0.623
|
3.90
|
49.72
|
50.2
|
6
|
4.12
|
3.36
|
0.898
|
3.74
|
47.70
|
52.3
|
7
|
3.44
|
2.50
|
0.778
|
3.21
|
41.00
|
59.0
|
8
|
3.93
|
3.29
|
1.021
|
3.22
|
41.01
|
58.9
|
9
|
3.54
|
2.87
|
0.991
|
2.89
|
36.81
|
63.1
|
Figure2: showing SEM image of preheated sample (acicular urea space holder)
Sintering is done after preheating to give the strength and to develop metallurgical bonding within the steel matrix. The preheated part is heated below its melting point but higher than the preheating temperature. Due to high temperature heating, bonding between the stainless steel particles takes place which gives strength to the preheated compact.
Table3: showing various measurement data of sintered foam samples (acicular urea space holder)
Sample no
|
% S.S.
|
%Urea
|
Weight
(gm)
|
Dia.(mm)
|
Height
(mm)
|
Density (gm/cm3)
|
% density
|
% porosity
|
1
|
90
|
10
|
3.60
|
9.92
|
10.13
|
4.60
|
58.60
|
41.4
|
2
|
90
|
10
|
4.24
|
9.91
|
11.70
|
4.70
|
59.87
|
40.13
|
3
|
90
|
10
|
3.89
|
9.80
|
10.53
|
4.90
|
62.42
|
37.58
|
4
|
84
|
16
|
3.64
|
9.85
|
12.52
|
3.815
|
48.59
|
51.41
|
5
|
84
|
16
|
2.66
|
9.72
|
9.15
|
4.056
|
51.67
|
48.33
|
6
|
84
|
16
|
3.28
|
9.87
|
11.03
|
3.886
|
49.51
|
50.49
|
7
|
80
|
20
|
3.19
|
9.83
|
12.60
|
3.336
|
42.49
|
57.51
|
8
|
80
|
20
|
2.76
|
9.86
|
12.07
|
2.996
|
38.16
|
61.84
|
9
|
80
|
20
|
2.71
|
9.85
|
11.05
|
3.218
|
40.99
|
59.01
|
After the sintering process is complete, the samples attained higher strength. Due to sintering process, the pore walls strengthens and the porosity is obtained in the samples. During the process of sintering the volume of the sample will shrink, although sometime it will expand due to the existence of internal stress produced in the compaction. The pores produced after sintering are smaller than that of the pores obtained after preheating. The greater driving force during sintering causes the pores to shrink to smaller size.
Figure3: showing SEM image of sintered sample (acicular urea space holder)
The pores obtained were acicular in shape. There are some pores which are circular in shape since the high driving force acts on pore walls at the sharp curvature regions of the acicular pores during sintering.
Fig 4. showing True stress and True strain curve (acicular urea sample)
The compressive behavior of cellular metals is very interesting due to their high energy absorption capacity. The pores in this sample are acicular and large. It is observed that the foam samples with 40% porosity doesn’t show any plateau stress as in aluminum foams due to larger young modulus, larger strain hardening & fcc structure (ductility) of austenitic stainless steel. The plateau region is obtained once the porosity is increased to 50 vol %. The plateau strength is approx. 80 MPa at 50% porosity. When the porosity is increased to 60 vol %, plateau strength decreased to approx. 45 MPa. The reason for high porosity foams to show plateau stress at a constant stress level is due to decrease in material content (large size of the acicular pores after sintering) & decreasing ductility. During plateau region, the elasto–plastic collapsing, yielding and bending deformation occurs before final densification process. With increasing porosity plateau stress decreases, since lesser force is required to densify the foam.
Future Scope
- By varying the compaction pressure we can observe the changes in microstructure and mechanical properties of the resulting foams with different porosity. Resulting applications should also be discussed.
- The changes in true stress -strain diagram by varying the strain rate can also prove to be beneficial.
- While using different shaped space holder, microstructural changes could be observed.
- The sintering atmosphere variation may also prove to be an asset resulting in different bond strength between steel particles.
- Sintering temperature change can also produce better pore morphology in steel foams.
- Change in foam sample shape by using different space holder could also be done to produce better results.
Conclusion
- Stainless steel foams can be fruitfully produced through powder metallurgy using urea as space holder.
- The porosity level can be varied with the amount of space holder used.
- The sintering should be done in vacuum to prevent the oxide formation during sintering.
- The pore morphology depends on the space holder used, sintering temperature and sintering time.
- The stress-strain curves of compression have two stages of deformation, which consist of a linear elastic region at the beginning of deformation and a long plateau/ plastic stage.
- The foam samples having larger acicular pores showed plateau regions at 50 and 60 vol. % porosity.
- The processed acicular high porosity foams delineated distinct plateau regions which show their impact energy absorbing characteristics where as with low porosity can be utilized in high strength structural applications.
Acknowledgements
The author thank CSIR-AMPRI, Bhopal & MANIT, Bhopal for supporting during the study.
References
- L.J. Gibson and M.F. Ashby, Cellular solids: structure and properties. 2nd ed.(CambridgeUniversity Press, Cambridge, 1997).
CrossRef
- J. Banhart // Prog. Mater. Sci. 46(2001) 559.
CrossRef
- H.P. Degischer and B. Kriszt, Handbook of cellular metals: production, processing, applications(Wiley-VCH Verlag, Weinheim, 2002).
CrossRef
- M. F. Ashby, A. Evans, N. A. Fleck, L.J. Gibson, J. W. Hutchinson and H. N. G. Wadley, Metal Foams – A Design Guide, Butterworth-Heinemann, Oxford, UK 2000.
- J. Banhart, M. F. Ashby, N. A. Fleck (Eds.), Cellular Metals and Metal Foaming Technology, International Conference on Cellular Metals and Metal Foaming Technology, Bremen, Germany, June 18-20, 2001, Verlag MIT Publishers, Bremen, Germany.
- T. Miyoshi, M. Itoh, S. Akiyama and A. Kitahara, Adv. Eng. Materials 2,2000, pp. 179-183.
CrossRef
- Ashby, M.F., Evans, A., Fleck, N.A., Gibson, L., Huthinson, J.W., Wadley, H., “Metal foams: a design guide”, Butterworth-Heinemann, 2000.
- Wadley, H.N.G., “Cellular metals manufacturing”, Advanced Engineering Materials, v. 4, pp. 726-733, 2002.
CrossRef
- MIYOSHI T., ITOH M., AKIYAMA S., KITAHARA A., Proc. MRS Symp. D. S. Schwartz, D. S. Shih, A. G. Evans, H. N. G. Wadley (Eds.), 521 (1998), 133.
- IP S.W., WANG Y., TOGURI J.M., Can. Met. Quart., 38 (1999), 81.
- DEQING W., ZIYUAN S., Mater. Sci. Eng. A, 361 (2003), 45.
- LLYOD D.J., MCLEOD A.D., MORRIS P.L., JIN I., Int. Patent (1991), WO 91/19823.
- WAAG U., SCHNEIDER L., LOETHMANN P., STEPHANI G., Metal Powder Rep., 55 (2000), 29.
- ZHAO Y.Y., SUN D.X., Scripta Mater., 44 (2001), 105.
- CHOU K.S., SONG M.A., Scipta Mater., 46 (2002), 379.
- ZHAO Y.Y., FUNG T., ZHANG L.P., ZHANG F.L., Scipta Mater., 52 (2005), 295.
- WADA T., INOUE A., Mater. Trans., 44 (2003), 2228.
- JIANG B., ZHAO N.Q., SHI C.S., DU X.W., LI J.J., MAN H.C., Mater. Lett., 59 (2005), 3333.
- WEAIRE D., Adv. Eng. Mater., 4 (2002), 723.
CrossRef
- BANHART J., BAUMGAERTENER F., COX S.J., KRONBERG B., LANGEVIN D., ODENBACH S., WEAIRE D.,WUEBBEN T., Proc. 1st Int. Symp. Microgravity Research and Applications in Physical Sciences and Biotechnology, ESA Publications, ESTEC, Noordwijk, 2001, p. 589.
- WUEBBEN T., ODENBACH S., BANHART J., Proc. Eurofoam 2000 P. Zitha, J. Banhart, G. Verbist, (Eds.), MIT-Verlag Bremen, 2000, pp. 98–103.
- WUEBBEN T., STANZICK H., BANHART J., ODENBACH S., J. Phys.: Cond. Matter, 15 (2003), S427.
- C.J.Yu, H.H Eifert, M.knuwer, M.Weber, and J. Baumeister, Investigation for the selection of Foaming Agents to produce Steel Foams, Porous and Cellular Materials for Structural Application MRS Symposium Proceedings Vol.521,145(1998).
- J.Banhart, J. Barumeister ,M.Weber, Powder Metallurgical Technology for the Production of Metal Foam ,Proc.European Conf. on Advanced PM Materials ,Birmingham ,p.201 (oct. 23-25 ,1995).
- Jiang B, Zhao NQ, Shi CS, Du XW, Li JJ and Man HC. 2005. A novel method for making open cell aluminum foams by powder sintering process. Mater Lett. 59: 3333-3336.
CrossRef
- Surace R, De Filippis LAC, Ludovico AD and Boghetich G. 2009. Influence of processing parameters on aluminium foam produced by space holder technique. Mater Design. 30: 1878-1885.
CrossRef
- Gulsoy HO and German RM. 2008. Sintered foams from precipitation hardened stainless steel powder. Powder Metall. 51: 350-353.
CrossRef
- Yang YJ, Han FS, Yang DK and Zheng K. 2007. Compressive behaviour of open cell Al-Al2O3 composite foams fabricated by sintering and dissolution process. Mater Sci Technol. 23: 502-504.
CrossRef
- Tuncer N and Arslan G. 2009. Designing compressive properties of titanium foams. J. Mater Sci. 44: 1477-1484.
CrossRef
- B.Wang, D.He and G.Shu, In: Metal Foams and Porous Metal Structures(MIT Verlag,2001), p. 351.
- T.G. Nieh, K. Higashi and J. Wadsworth //Materials Science and Engineering A. 283(2000) 105.
CrossRef
- Kenneth Kremer, Anthony Liszkiewicz and James Adkins. DEVELOPMENT OF STEEL FOAM MATERIALS AND STRUCTURES. The United States Department of Energy And American Iron and Steel Institute (2004)
- Degischer, H.P. & Kriszt, B. (Ed(s).) (2002). Handbook of Cellular Metals, Wiley-VCH, ISBN 3-527-30339-1, Weinheim
Views: 1,564
This work is licensed under a Creative Commons Attribution 4.0 International License.