S. R. Kumbhar1*, Subhasis Maji1 and Bimlesh Kumar2
¹School of Engineering and Technology (SOET), IGNOU, New Delhi - 110 068, India.
²J.T. Mahajan College of Engineering Faizpur - 425 424, India.
DOI : http://dx.doi.org/10.13005/msri/090115
Article Publishing History
Article Received on : 10 Apr 2012
Article Accepted on : 28 May 2012
Article Published :
Plagiarism Check: No
Article Metrics
ABSTRACT:
Smart materials are materials with properties that can be significantly altered in a controlled fashion by external stimuli, such as stress, temperature, pH, moisture, electric or magnetic fields. An elastomer comprising a matrix interspersed with micron sized ferromagnetic particles is known as a Magnetorheological Elastomer (MRE). The rheological properties of MREs are altered by the application of an external magnetic field. The characteristic response of MRE is influenced by many factors including; the elastomer matrix, the size, distribution, composition and percentage volume of the ferromagnetic particles, and whether the ferromagnetic particles are aligned in chains or randomly dispersed. During the past two decades the interest in intelligent material based solutions has shown a huge growth. Present work deals with the study of preparation method of Magnetorheological Elastomer mould and testing for its dynamic behaviour. Micron size iron particles are used for the preparation of MRE in order to increase number of iron particles in elastomer matrix. Two different types of MRE moulds are prepared and their dynamic response has been studied. Comparison has been done between MRE mould cured with magnetic field and without magnetic field by testing them with and without application of magnetic field. The results obtained are satisfactory and can be applied for automotive sector to reduce noise and vibrations.
KEYWORDS:
Smart material; MRE; Curing; Spring constant; Response analysis
Copy the following to cite this article:
Kumbhar S. R, Maji S, Kumar B, Fabrication and Response Analysis of Magnetorheological Elastomer. Mat.Sci.Res.India;9(1)
|
Introduction
Smart materials are materials with properties that can be significantly altered in a controlled fashion by external stimuli, such as stress, temperature, pH, moisture, electric or magnetic fields. Especially materials, which can respond to the changes in their environment in a very short time, are currently developed. An elastomer comprising a matrix interspersed with micron sized ferromagnetic particles is known as a Magnetorheological Elastomer (MRE). The rheological properties of MREs (the deformation and flow behaviour under stress) are altered by the application of an external magnetic field.1 The characteristic response of MRE is influenced by many factors including; the elastomer matrix, the size, distribution, composition and percentage volume of the ferromagnetic particles, and whether the ferromagnetic particles are aligned in chains or randomly dispersed. MRE’s are used to change the natural frequency of the system by changing the stiffness of the structure. During the past two decades the interest in intelligent material based solutions has shown a huge growth. In this study dynamic response of the MRE mould has been presented. Comparison has been done between MRE mould cured with magnetic field and without magnetic field by testing them with and without application of magnetic field.
Preparation Of MRE
Full-proof process for MRE preparation is not given anywhere in previous literature. So trial and error method was used in order to get solid mould. Different types of rubbers available in market. Selection of particular rubber depends on its properties and availability. Here Sylgard’s 184 silicone elastomer was selected for the preparation of moulds. Initially normal rubber was used for mould preparation in order to study curing procedure because Sylgard’s184 silicone elastomer is much costlier. It was observed that as material combination changes curing time and properties of final mould also changes. In some cases even solid mould was not formed even after heating or curing mould for 48 hours. By taking lots of efforts and observation under expert guidance following fabrication procedure was finalised for preparation of MRE mould using Sylgard’s184 silicone elastomer.
We successfully prepared eight moulds (Figure I). Mould No.1 is prepared by using sylgard’s rubber in order to study curing process presence of magnetic field. Mould No.2 is prepared to study effect of heat on Sylgard’s 184 silicone elastomer it is transparent because of absence of magnetic particles.[2,3,4]
Two types of moulds were prepared for testing like –
MRE Mould prepared by using Sylgard’s 184 silicone elastomer and cured in magnetic field i.e. 184 mMRE (4 Nos.).
MRE Mould prepared by using Sylgard’s 184 silicone elastomer and cured without magnetic field i.e. 184 nMRE (4 Nos.).
Testing of MRE MOULD
Dynamic response of two moulds, i.e. 184 mMRE and 184 nMRE has been studied. Test set up6 required for testing this MRE moulds was fabricated (Figure II) along with various instruments like accelerometers, FFT analyzer, Data acquisition and analysis software. This set up also includes the exciter, base plate and accelerometer. MRE mould was accommodated in aluminum housing with two magnetic poles M1 and M2. Load was applied over top surface of MRE mould. This load applied was constant for all mould readings. Accelerometer was mounted over the load indicating vibration level in absence of magnetic field and in presence of magnetic field for both types of MRE moulds. A magnetic field of 0.7 T was applied both sides for getting MRE effects. We tested 8 (4 nMRE and 4 mMRE) mould for investigating their dynamic response behaviour.
Results and Discussion
During testing various data were recorded and from that the frequency responses (acceleration versus frequency) of 184 nMRE and 184 mMRE were plotted.
Experimental Results for 184 Nmre
The frequency response for the MRE cured without magnetic field (184 nMRE) is shown in Figure III & IV with and without application of magnetic field. Each graph contains plot of acceleration versus frequency. X coordinator of cursor value at right side of each figure indicates natural frequency of 184 nMRE at that particular condition. The natural frequency without magnetic field is indicated by f0 and the same with magnetic field is indicated by f1.
Experimental Results for 184 MMRE
The frequency response for the MRE cured with magnetic field (184 mMRE) is shown in Figure V and VI with and without application of magnetic field. Each graph contains plot of acceleration versus frequency. X co-ordinator of cursor value at right side of each figure indicates natural frequency of 184 mMRE at that particular condition.
From the graphs values of frequencies f0 and f1 for various other moulds were obtained. Percentage changes in resonant frequency were calculated, keeping load constant for all the mould conditions, from obtained frequencies and summarised in Table I.
According to Jolly et.al.,,5 for an MRE experiencing a shear force, fractional change in modulus ΔG/G0 is related to the fractional change in natural frequency Δω/ω0, using
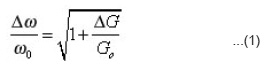
Solving for fractional change in modulus yields,
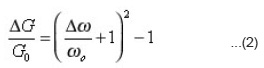
Assuming that the equation for the shear modulus can be applied to the elastic modulus when the stress is applied uniaxial to the material, we obtain the values for the fractional change in modulus these values are shown in Table II.
From Table I, it is clear that for 184 nMRE, the average change of natural frequency is 122.5 Hz with worst case value of 64 Hz and average percentage change for the mMRE is 15.37 % with worst case value of 6 %
For 184 mMRE, the average change of natural frequency is 136 Hz with worst case value of 64 Hz and average percentage change for the mMRE is 15.60 % with worst case value of 7 %.
From Table II, it is clear that for nMRE has an average change in modulus is 779.60 with average worst case value of 402.4 and average percentage change for the mMRE is 34.18 % with worst case value of 13.47 %.
For 184 mMRE, the average change of natural frequency is 764.04 Hz with worst case value of 40.18 Hz and average percentage change for the mMRE is 34.09 % with worst case value of 14.78%.
These results show that aligning the iron beads while elastomer cures allows the applied magnetic field to have a greater effect on the change in modulus. From these it is clear that as we change the size of iron particles, it affects on the natural frequency when magnetic field is applied. The response of 184 mMRE to applied magnetic field is remarkable as compared with 184 nMRE. Also it is observed that natural frequency of 184 mMRE is always greater than that of 184 nMRE.
Table 1: Fractional Change in Resonant Frequency
Table 2: Result table of fractional change in resonant frequency
Figure 1: Prepared MRE Moulds
Figure 2: Test Set for Dynamic Response Analysis of MRE mould
Figure 3: Response of 184 nMRE Without Magnetic Field (Mould No.1)
Figure 4: Response of 184 nMRE With Magnetic Field (Mould No.1)
Figure 5: Response of 184 mMRE Without Magnetic Field (Mould No.5)
Figure 6: Response of 184 mMRE Without Magnetic Field (Mould No.5)
Conclusion
The results obtained in this study shows that aligning the iron beads while elastomer cures allow the applied magnetic field to have a greater effect on the change in modulus. Also MR Elastomer gives satisfactory response to applied magnetic field. Its resonant frequency and modulus of elasticity varies with magnetic field. This characteristic of MRE mould could become important feature in automotive sector for reducing noise and vibrations.
References
- C. Ruddy, E. Ahearne and G. Byrne, Advanced Manufacturing Science (AMS) Research Centre, Mechanical Engineering, University College Dublin, Belfield, Dublin 4, Ireland (2007).
- Hua-xia Deng, Xing-long Gong, Journal of Nonlinear Science and Numerical Simulation, Vol.13 (2008).
- H. Bose and R. Roder, 11th International Conference on Electrorheological Fluids and Magnetorheological Suspensions, Dresden, (2008).
- Wei Ke-xiang, Meng Guang, Zhang Wen- ming, Zhu Shi-sha, J. Cent. South Univ. Technology, Vol.15 (2008).
- M.R.Jolly, J.D.Carlson, B.C.Munoz, T.A.Bullians, Journal of Intelligent Material Systems and Structures, Vol.7 (1996).
- Michael Henri, M.S. Thesis, Simon Fraser University, (2005).

This work is licensed under a Creative Commons Attribution 4.0 International License.