Introduction
Concrete
Concrete is an integrated material that is mostly made up of water, aggregate, and cement. Over time, the cement forms a robust matrix that binds the other ingredients together, resulting in a durable, rigid material with diverse applications such as in buildings and pavements. The utilization of concrete on a large scale was pioneered by the ancient Romans, with the technology playing a significant role in the construction of structures like the Colosseum in Rome8.
Concrete technology experienced a revival in the modern era, and today. Its versatility and strength make it a cornerstone in construction and infrastructure projects worldwide.
Historical background
Concrete has a rich history dating back thousands of years, with its evolution closely tied to the development of civilizations. Here is a brief overview of the history and background of concrete:
Ancient Civilizations
Egyptian and Mesopotamian Use: Early forms of concrete-like materials were used by ancient civilizations such as the Egyptians and Mesopotamians. They utilized a mixture of mud and straw to create early construction materials.
Roman Advancements: The Romans made significant advancements in concrete technology around 300 BC. They used a blend of volcanic ash, lime, and seawater to create a durable concrete-like substance that played a crucial role in the construction of structures like the Colosseum and the Pantheon.
Roman Decline to Renaissance
Decline of Concrete Use: With the fall of the Roman Empire, concrete technology experienced a decline during the medieval period. The knowledge and techniques for producing high-quality concrete were lost, and alternative building methods, such as timber framing, became more prevalent.
Renaissance Rediscovery: In the Renaissance era, there was a resurgence of interest in classical knowledge and architecture. This led to a rediscovery of Roman concrete techniques, and there was a renewed focus on experimenting with concrete formulations.
Industrial Revolution
Reintroduction of Concrete: The Industrial Revolution in the 18th and 19th centuries brought about technological advancements, and concrete experienced a revival. The development of Portland cement in the 19th century, a key component in modern concrete, played a pivotal role in the widespread use of concrete.
20th Century to Present
Modern Concrete Technology: The 20th century saw continuous innovation in concrete technology. Reinforced concrete, where steel is embedded to enhance tensile strength, became widely used for various structural applications.
Advancements in Materials: Research and development led to the introduction of various admixtures, aggregates, and supplementary cementitious materials, further enhancing. HSC, SSC, and sustainable concrete practices are among the developments in recent decades.
Ongoing research and advancements continue to shape the future of concrete technology, with a focus on sustainability, durability, and performance.
Properties of concrete
Concrete is a versatile construction material known for its durability, strength, and adaptability. The properties of concrete are influenced by its constituent materials, mix proportions, and curing conditions12. Here are some key points:
Compressive Strength
Definition: The ability of concrete to withstand axial loads or pressure.
Significance: Compressive strength is a critical property, indicating how well concrete can resist crushing forces.
Tensile Strength
Definition: The ability of concrete to resist tension forces.
Significance: While concrete is weak in tension, the addition of reinforcement (as in reinforced concrete) enhances its tensile strength.
Flexural Strength
Definition: The ability of concrete to resist bending or deformation.
Significance: Important for elements subjected to bending, such as beams and slabs.
Workability
Definition: The ease with which concrete flow.
Significance: Workability affects construction processes and the quality of the final product.
Durability
Definition: The capability to resist deterioration over time due to environmental factors.
Significance: Durability is crucial for long-term performance, especially in harsh conditions.
Permeability
Definition: The penetration of liquids and gases.
Significance: Low permeability is essential for structures exposed to water or aggressive chemicals.
Density
Definition: The mass per unit volume of concrete.
Significance: Density affects the weight of structures and influences buoyancy in underwater constructions.
Setting Time
Definition: The time taken by concrete to solidify and harden.
Significance: Setting time influences construction schedules and affects the handling of fresh concrete.
Shrinkage
Definition: The reduction in volume of concrete as it dries and hardens.
Significance: Shrinkage can lead to cracking, and its control is crucial for maintaining structural integrity.
Heat of Hydration
Definition: The heat generated during the chemical reaction between cement and water.
Significance: Excessive heat can affect the properties of concrete, and control measures are employed to manage it.
Abrasion Resistance
Definition: The ability of concrete to withstand wear and erosion.
Significance: Important for surfaces subjected to heavy traffic or abrasive forces.
Thermal Properties
Definition: The ability of concrete to conduct and store heat.
Significance: Relevant in applications where thermal insulation or conductivity is a consideration.
Understanding and optimizing these properties allow engineers and builders to tailor concrete mixes to meet specific project requirements, ensuring the durability and performance of structures over their service life.
Lightweight concrete
Lightweight concrete, also known as lightweight aggregate concrete, is a type of concrete that incorporates lightweight aggregates or lightweight materials to achieve a lower density compared to traditional concrete10. This type of concrete offers various benefits, including reduced structural load, improved insulation properties, and enhanced workability. Here are key aspects of lightweight concrete: It is important to select the appropriate lightweight aggregate and mix design based on the specific requirements of each project17.
Applications
Precast Elements: Its reduced weight makes it suitable for precast concrete elements, facilitating easier transportation and installation.
Fire Resistance
Enhanced Fire Resistance: Lightweight concrete can offer improved fire resistance due to the insulating properties of certain lightweight aggregates.
Reduced Structural Load
Advantageous in High-Rise Buildings: In high-rise structures, where the reduction of structural load is crucial, lightweight concrete can be a preferred choice.
Cost Considerations
Material Costs: While lightweight aggregates may be more expensive than traditional aggregates, the overall cost-effectiveness of lightweight concrete depends on factors such as transportation and installation savings.
Construction waste in India
Construction waste in India poses significant environmental and sustainability challenges, reflecting the rapid urbanization and infrastructure development in the country. Here are key aspects related to construction waste in India1, 18:
Waste Management Practices
Challenges: Effective construction waste management practices are often challenging to implement due to factors such as inadequate infrastructure, lack of awareness, and limited enforcement of regulations.
Recycling Initiatives: Some construction and demolition waste recycling initiatives have emerged in certain urban centers, but their scale and impact vary.
Environmental Impact
Landfilling: Construction waste often ends up in landfills, contributing to land degradation and the loss of valuable space.
Air and Water Pollution: Improper disposal methods can result in air and water pollution, posing risks to ecosystems and public health.
Quantities of Waste
Rapid Urbanization: India’s ongoing urbanization and infrastructure development have led to an increase in construction activities, resulting in higher volumes of construction waste.
Building Demolition: The demolition of older structures, particularly in urban areas, contributes significantly to construction waste.
Tile aggregate concrete
(Miličević, Štirmer, and Banjad Pečur 2016)”Tile aggregate concrete” typically refers to concrete that incorporates crushed tiles as a partial replacement for traditional coarse aggregates. This practice is a form of sustainable construction, as it utilizes recycled or waste materials, like discarded tiles, to reduce the environmental impact of construction activities. Here are key aspects related to tile aggregate concrete.
Tile aggregate concrete has both environmental and economic benefits.
Waste Reduction and Recycling
Reuse of Waste Tiles
Incorporating crushed or recycled tiles as aggregates diverts waste materials from landfills, contributing to reduced environmental impact.
Resource Conservation
Recycling tiles conserves natural resources by decreasing the demand for traditional coarse aggregates.
Energy Savings
Reduced Extraction
Using recycled tiles in concrete reduces the need for extracting new raw materials, resulting in energy savings and lower environmental disturbance associated with aggregate mining.
Lower Carbon Footprint
Reduced Transportation Emissions
Utilizing locally sourced waste tiles reduces transportation distances for materials, leading to lower carbon emissions associated with material transportation.
Literature Review
To manufacture concrete from tile waste, replacement with 20 mm along the range, tile waste with “0%, 5%, 10%, 15%, 20%, and 25%,” and fly ash was used to partially replace cement. Roof tile aggregate concrete achieves its average maximum compressive strength at a replacement rate of 25%.4
When normal concrete is used to replace 25% of the roof tile aggregate replacement, the strength drops by 10% to 15%. In most cases, replacing tiles with concrete is sufficient for minor structures.5
The ceramic debris that is embraced is broken tiles. The workability and “compressive and split tensile strengths of fresh concrete are determined after three, seven, and twenty-eight days”. According to the research, waste tile aggregate replacement should account for 5 to 30% of the total and can be used with typical mixes such as M15 and M20.7
The research focuses on waste ceramic from the Spanish industry. All technical standards established by current Spanish legislation were met. Up to 100% of the coarse aggregate is replaced with ceramic aggregates. Tests appropriate for comparing the mechanical qualities with traditional concrete were carried out. Similar to regular gravel concrete, the ceramic ware aggregate concrete demonstrated workable qualities.2
Materials and properties
Materials used
Tile aggregate concrete involves the use of crushed or recycled tiles as a substitute for traditional coarse aggregates (such as gravel or crushed stone) in the concrete mix. The choice of materials plays a crucial role in determining the properties and performance of tile aggregate concrete. Here are the key materials used in the production of tile aggregate concrete:
In the process of incorporating ceramic tiles as partial replacements for traditional aggregates in concrete, various key components contribute to the formulation and performance of tile aggregate concrete. Crushed or recycled tiles serve as a sustainable alternative to conventional aggregates. Derived from damaged or unused tiles obtained during construction or demolition projects, these tiles are crushed or broken into smaller pieces for use in concrete. The versatility of this approach extends to various tile types, including ceramic tiles, porcelain tiles, and other common construction tiles14. The binder in tile aggregate concrete is typically Portland cement. Playing a crucial role, cement binds the crushed or recycled tile aggregates together, facilitating the formation of a cohesive and hardened structure. This choice of binder is fundamental to the overall strength and durability of the resulting concrete.
Fine aggregates, such as sand, are introduced to the mix to enhance workability and fill voids between the tile aggregates. This addition not only contributes to the overall workability of the concrete but also ensures the cohesion of the mixture. Water serves a pivotal role in the concrete-making process. It is employed to hydrate the cement, initiating the chemical reaction essential for forming the concrete matrix. Maintaining a proper water-cement ratio is imperative, as it directly influences the desired strength and workability of the tile aggregate concrete. The thoughtful combination of these components showcases the adaptability and potential for innovation in the field of concrete construction using ceramic tile aggregates.15
It’s important to note that the specific types and proportions of these materials can vary based on the desired properties of the concrete, the application, and the availability of materials. The mix design is a critical aspect that needs to be carefully optimized to ensure the desired performance of tile aggregate concrete. Additionally, quality control measures are essential to maintain consistency in material properties and overall concrete performance.16
Table 1: Cement – Properties
SL.NO
|
Properties
|
Test results
|
IS:169-1989
|
1.
|
Normal consistency
|
0.32
|
|
2.
|
Initial setting time
|
50min
|
Minimum of 30min
|
3.
|
Final setting time
|
340min
|
Maximum of 600min
|
4.
|
Specific gravity
|
3.14
|
|
|
Compressive strength
|
1.
|
3daysstrength
|
29.2 Mpa
|
Minimum of 27Mpa
|
2.
|
7daysstrength
|
44.6 Mpa
|
Minimum of 40Mpa
|
3.
|
28daysstrength
|
56.6 Mpa
|
Minimum of 53Mpa
|
Table 2: Fine Aggregate – Properties
S.No
|
Description Test
|
Result
|
1
|
Sand zone
|
Zone-III
|
2
|
Specific gravity
|
2.59
|
3
|
Free Moisture
|
1%
|
4
|
Bulk density of fine aggregate (poured density)
|
1385.16kg/m3
|
5
|
Bulk density of fine aggregate (tapped density)
|
1606.23kg/m3
|
Table 3: Properties of Coarse Aggregate
S.No
|
Description
|
Test Results
|
1
|
Nominal size used
|
20mm blue metal
|
2
|
Specific gravity
|
2.9
|
3
|
Impact value
|
10.5
|
4
|
Water absorption
|
0.15%
|
5
|
Sieve analysis
|
20mm
|
6
|
Aggregate crushing value
|
20.19%
|
7
|
Bulk density of coarse aggregate(Poured density)
Bulk density of coarse aggregate (Tapped density)
|
1687.31kg/m3
1935.3kg/m3
|
Ceramic tile
Table 4: Ceramic Tile – Properties
S.No
|
Description
|
Test Results
|
1
|
Origin Rock
|
Feldspar
|
2
|
Impact value of crushed tiles
|
12.5%
|
3
|
Specific gravity of crushed tiles
|
2.6
|
4
|
Specific gravity of tile powder(C.F.A)
|
2.5
|
5
|
Water absorption of crushed tiles
|
0.19%
|
6
|
Water absorption of Tile powder(C.F.A)
|
0.13%
|
Granite powder
Table 5: Properties of Granite Powder
S.No
|
Description
|
Test Results
|
1
|
Specific gravity of granite powder
|
2.4
|
2
|
Water absorption of granite powder
|
0.10%
|
Mix design form M25 grade concrete
Final Mix Proportions
C
|
FA
|
CA
|
WATER
|
380
|
634
|
1339
|
175
|
1
|
1.67
|
3.52
|
0.4
|
For 20% CCA Aggregates
Mix Proportions
C
|
NFA
|
NCA
|
CCA
|
WATER
|
380
|
640
|
1074
|
241
|
174.5
|
1
|
1.7
|
2.83
|
0.63
|
0.44
|
Mix Proportions
|
|
|
|
|
C
|
NFA
|
NCA:
|
CCA
|
WATER
|
380
|
640
|
939
|
359
|
174.5
|
1
|
1.7
|
2.47
|
0.95
|
0.44
|
For 40% CCA Aggregates
Mix Proportions
C
|
NFA
|
NCA
|
CCA
|
WATER
|
380
|
640
|
802
|
479
|
174
|
1
|
1.7
|
2.11
|
1.25
|
0.44
|
For 50% CCA Aggregates
Mix Proportions
|
|
|
|
|
C
|
NFA
|
NCA
|
CCA
|
WATER
|
380
|
638
|
669
|
603
|
174
|
1
|
1.6
|
1.70
|
1.59
|
.44
|
For 10% CCA+10% CFA Aggregates
Mix Proportions
|
|
|
|
|
|
C
|
NFA
|
CFA
|
NCA
|
CCA
|
WATER
|
380
|
574
|
62
|
1207
|
120
|
174
|
1
|
1.51
|
0.16
|
3.18
|
0.31
|
0.44
|
For 20% CCA+10% CFA Aggregates
Mix Proportions
|
|
|
|
|
|
C
|
NFA
|
CFA
|
NCA
|
CCA
|
WATER
|
380
|
574
|
62
|
1074
|
240.7
|
174
|
1
|
1.51
|
0.16
|
2.83
|
0.63
|
0.44
|
For 30% CCA+10% CFA Aggregates
|
Mix Proportions
|
|
|
|
|
C
|
NFA
|
CFA
|
NCA:
|
CCA
|
:WATER
|
380
|
574
|
62
|
939
|
359
|
174.5
|
1
|
1.51
|
0.16
|
2.47
|
0.95
|
0.44
|
For 40% CCA+10% CFA Aggregates
|
Mix Proportions:
|
|
|
|
|
|
C
|
NFA
|
CFA
|
NCA
|
CCA
|
WATER
|
380
|
574
|
62
|
804
|
481
|
174
|
1
|
1.51
|
0.16
|
2.12
|
1.26
|
0.44
|
For 10% CCA+10% GP Aggregates
|
Mix Proportions
|
|
|
|
|
|
C
|
NFA
|
GP
|
NCA
|
CCA
|
:WATER
|
380
|
574
|
59
|
1207
|
120
|
173.5
|
1
|
1.51
|
0.15
|
3.18
|
0.31
|
0.44
|
For 20% CCA+10% GP Aggregates
Mix Proportions
|
|
|
|
|
|
C
|
NFA
|
GP
|
NCA
|
CCA
|
WATER
|
380
|
574
|
59
|
1071
|
240.7
|
173.5
|
1
|
1.51
|
0.15
|
2.81
|
0.63
|
0.44
|
For 30% CCA+10% GP Aggregates
|
Mix Proportions
|
|
|
|
|
|
C
|
NFA
|
GP
|
NCA
|
CCA
|
WATER
|
380
|
574
|
59
|
939
|
359
|
173.5
|
1
|
1.51
|
0.15
|
2.47
|
0.95
|
0.44
|
For 40% CCA+10% GP Aggregates
|
Mix Proportions
|
|
|
|
|
|
C
|
NFA
|
GP
|
NCA
|
CCA
|
WATER
|
380
|
574
|
59
|
804
|
481
|
173.5
|
1
|
1.51
|
0.15
|
2.12
|
1.26
|
0.44
|
Experimental details
General
By varying the ratio of “crushed tiles, crushed tile powder, and granite powder” substituted for coarse and fine aggregates, several blends were created. Together with standard mixes, a total of 14 other types of mixes are generated. In addition to using 10% of crushed granite and tile powder to replace the fine aggregate, “10%, 20%, 30%, 40%, and 50%” of the coarse aggregates are substituted with crushed tiles.
Table 6: Information about the substitution of aggregates in mix codes
S.no
|
Mix code
|
Cement
|
Coarse Aggregate %
|
Fine Aggregate %
|
Natural coarse aggregate
|
Crushed Tiles
|
sand
|
Crushed tile powder
|
Granite Powder
|
1
|
M0
|
100
|
100
|
0
|
100
|
0
|
0
|
2
|
M1
|
100
|
90
|
10
|
100
|
0
|
0
|
3
|
M2
|
100
|
80
|
20
|
100
|
0
|
0
|
4
|
M3
|
100
|
70
|
30
|
100
|
0
|
0
|
5
|
M4
|
100
|
60
|
40
|
100
|
0
|
0
|
6
|
M5
|
100
|
50
|
50
|
100
|
0
|
0
|
7
|
M6
|
100
|
90
|
10
|
90
|
10
|
0
|
8
|
M7
|
100
|
80
|
20
|
90
|
10
|
0
|
9
|
M8
|
100
|
70
|
30
|
90
|
10
|
0
|
10
|
M9
|
100
|
60
|
40
|
90
|
10
|
0
|
11
|
M10
|
100
|
90
|
10
|
90
|
0
|
0
|
12
|
M11
|
100
|
80
|
20
|
90
|
0
|
10
|
13
|
M12
|
100
|
70
|
30
|
90
|
0
|
10
|
14
|
M13
|
100
|
60
|
40
|
90
|
0
|
10
|
Workability
The quality of freshly mixed concrete that can be determined by measuring the material and the final product’s look is workability. The following three techniques can be used to assess.
Slump-Cone Test
In order to determine the workability in a precise amount to create a homogenous mixture.
Compaction factor test
Apparatus
The compaction factor apparatus includes trowels, a hand scoop (15.25 cm long), a steel rod (1.6 cm in diameter, 61 cm long, rounded at one end), and a balance. Compaction factor= (W2-W1)/(W3-W1)
Compressive Strength for the cube strength
After preparing the concrete according to the specifications, create the specimen by placing it into the appropriate mould shape—a 15 cm by 15 cm by 15 cm cube—and properly compacting it. After 24 hours, place the specimen in water to cure.
Procedure of Split-Tensile
After preparing the concrete according to the specifications, create the specimen by placing it into the appropriate mould shape—a 15 cm by 15 cm by 15 cm cube—and properly compacting it. After 24 hours, place the specimen in water to cure.
Flexural strength test
After preparing the concrete according to the specifications, create the specimen by filling the mould in the appropriate shape—a 10x10x50 cm prism—and properly compacting it. After a day, place the specimen in water to cure.
Test results
WORKABILITY: The perfect concrete is one that can be prepared, put, compacted, and moulded with ease and under all circumstances. The two approaches used to evaluate the workability in this chapter are as follows:
Test of Slump Cones
The test was run on recently mixed concrete that had not yet been moulded. At various times, a total of fourteen concrete mixes are created.
Table 7: Test results from slump cone test for workability in mm
S.No
|
Mix Designation
|
Aggregate Replacement
(CCA+CFA+GP)
|
Workability (mm)
M25
|
1
|
M0
|
0+0+0
|
62
|
2
|
M1
|
10+0+0
|
65
|
3
|
M2
|
20+0+0
|
68
|
4
|
M3
|
30+0+0
|
73
|
5
|
M4
|
40+0+0
|
78
|
6
|
M5
|
50+0+0
|
81
|
7
|
M6
|
10+10+0
|
63
|
8
|
M7
|
20+10+0
|
67
|
9
|
M8
|
30+10+0
|
71
|
10
|
M9
|
40+10+0
|
76
|
11
|
M10
|
10+0+0
|
72
|
12
|
M11
|
20+0+0
|
79
|
13
|
M12
|
30+0+0
|
86
|
14
|
M13
|
40+0+0
|
102
|
Compaction Factor Test
The same mix that underwent a slump cone test for workability was used for the compaction factor.
Table 8: Workability Test Report
S.No
|
Mix Designation
|
Aggregate Replacement
(CCA+CFA+GP)
|
Workability (mm)
M25
|
1
|
M0
|
0+0+0
|
0.82
|
2
|
M1
|
10+0+0
|
0.84
|
3
|
M2
|
20+0+0
|
0.855
|
4
|
M3
|
30+0+0
|
0.87
|
5
|
M4
|
40+0+0
|
0.89
|
6
|
M5
|
50+0+0
|
0.93
|
7
|
M6
|
10+10+0
|
0.83
|
8
|
M7
|
20+10+0
|
0.86
|
9
|
M8
|
30+10+0
|
0.88
|
10
|
M9
|
40+10+0
|
0.91
|
11
|
M10
|
10+0+0
|
0.85
|
12
|
M11
|
20+0+0
|
0.90
|
13
|
M12
|
30+0+0
|
0.93
|
14
|
M13
|
40+0+0
|
0.95
|
Compressive strength
Subsequently the workability tests, 42 cubes of size 150 x 150 x 150mm were produced and subjected to testing for 7 days, 14 days, and 28 days on each of 13 specimens.
Table 9: Results of M25 grade concrete’s compressive strength after 7, 24, and 28 days.
S.No
|
Mix Designation
|
Aggregate Replacement
(CCA+CFA+GP)
|
Compressive strength of M25 Grade concrete
|
7 days
|
14 days
|
28 days
|
1
|
M0
|
0+0+0
|
20.57
|
28.54
|
33.18
|
2
|
M1
|
10+0+0
|
24.09
|
31.39
|
36.50
|
3
|
M2
|
20+0+0
|
26.27
|
32.8
|
39.50
|
4
|
M3
|
30+0+0
|
28.05
|
37.53
|
43.14
|
5
|
M4
|
40+0+0
|
23.96
|
31.77
|
37.16
|
6
|
M5
|
50+0+0
|
22.22
|
28.88
|
34.18
|
7
|
M6
|
10+10+0
|
21.98
|
29.00
|
35.17
|
8
|
M7
|
20+10+0
|
23.41
|
31.60
|
37.16
|
9
|
M8
|
30+10+0
|
26.50
|
34.40
|
39.50
|
10
|
M9
|
40+10+0
|
20.01
|
26.65
|
32.90
|
11
|
M10
|
10+0+0
|
21.05
|
28.64
|
34.50
|
12
|
M11
|
20+0+0
|
24.60
|
33.58
|
39.50
|
13
|
M12
|
30+0+0
|
28.10
|
38.40
|
42.14
|
14
|
M13
|
40+0+0
|
21.32
|
28.09
|
33.84
|
Split Tensile strength
The split tensile strength achieved by testing the cylindrical specimen for M25 grade concrete to all the mixes specified for various replacements is as follows:
Table 10: Results of split tensile strength for concrete of grade M25
S.No
|
Mix Designation
|
Aggregate Replacement
(CCA+CFA+GP)
|
Split Tensile strength of M25 Grade concrete
|
7 days
|
14 days
|
28 days
|
1
|
M0
|
0+0+0
|
1.67
|
2.18
|
2.56
|
2
|
M1
|
10+0+0
|
1.67
|
2.19
|
2.61
|
3
|
M2
|
20+0+0
|
1.69
|
2.24
|
2.61
|
4
|
M3
|
30+0+0
|
1.71
|
2.26
|
2.65
|
5
|
M4
|
40+0+0
|
1.69
|
2.21
|
2.59
|
6
|
M5
|
50+0+0
|
1.67
|
2.16
|
2.52
|
7
|
M6
|
10+10+0
|
1.69
|
2.18
|
2.57
|
8
|
M7
|
20+10+0
|
1.69
|
2.21
|
2.61
|
9
|
M8
|
30+10+0
|
1.70
|
2.23
|
2.64
|
10
|
M9
|
40+10+0
|
1.65
|
2.19
|
2.50
|
11
|
M10
|
10+0+0
|
1.68
|
2.20
|
2.58
|
12
|
M11
|
20+0+0
|
1.71
|
2.21
|
2.65
|
13
|
M12
|
30+0+0
|
1.72
|
2.24
|
2.66
|
14
|
M13
|
40+0+0
|
1.69
|
2.202.56
|
2.62
|
Flexural Strength
Table 11: Flexural test results for 7, 14 and 28 days
S.No
|
Grade Concrete
|
Mix Code
|
Flexural strength in N/mm2
|
7 days
|
14 days
|
28 days
|
1
|
M25
|
M0
|
7.92
|
8.98
|
9.95
|
2
|
M25
|
M3
|
8.88
|
9.15
|
10.28
|
Discussion
Workability
Slump Cone Test
According to the results, the workability of mixes is raised by 4.8%, 9.6%, 17.7%, 25.8%, 30.6%, 1.6%, 8%, 14.5%, 22.5%, 16.1%, 27.4%, 38.7%, and 64.5% over typical M25 concrete grade (M0).
Compaction Factor Test
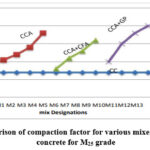 |
Figure 15: Comparison of compaction factor for various mixes with conventional concrete for M25 grade
Click here to View Figure
|
According to the findings, the workability of the mixes is raised by 2.4%, 4.3%, 6.1%, 8.5%, 13.4%, 1.2%, 4.9%, 7.3%, 10.9%, 3.6%, 9.7%, 13.4%, and 15.8% and 64.5%, respectively, over the ordinary M25 concrete grade (M0).
Compressive strength
When comparing the strengths of all mixtures, M3, M8, and M12 have the greatest, with 30% coarse aggregate replacement. The inclusion of granite powder improves both strength and workability.
Split tensile strength
When concrete is compared to ordinary concrete after 28 days of curing, the split tensile strength varies as follows: 1.95 percent, 5%, 7%, 1.18%, -1.6%, 0.39%, 1.9%, 3.1%, -2.3%, 0.78%, 3.5%, 3.9%, and 2.3%.
Flexural Test
The beam’s strength increases in a linear fashion. For the three grades, the strength variation is growing. The strength gain after seven days is nearly the same for all three grades, however after fourteen days, M25’s strength grows more quickly. Although we are not comparing this concrete to regular concrete, the strength achieved is still acceptable.
Discussion
The partial replacement of traditional aggregates with ceramic tiles in concrete is an innovative approach gaining attention in the construction industry. Similar studies and research have explored the impact of incorporating alternative materials into concrete mixes to enhance properties such as strength, durability, and sustainability.
The study investigated the use of recycled ceramic aggregates in concrete production. The findings indicated that the incorporation of ceramic aggregates led to improved compressive strength compared to traditional concrete mixes. This aligns with our study’s results, where the 28-day compressive strength of 56.6 MPa exceeded the minimum requirement of 53 MPa.9
The study delved into the environmental aspects of using recycled materials in concrete. Their life cycle assessment revealed a reduction in carbon footprint when recycled materials were employed. Our study aligns with this sustainability focus, as the use of crushed or recycled ceramic tiles reflects a commitment to reducing waste and promoting eco-friendly construction practices.3
The study explored the influence of different binders on the performance of ceramic-based concrete. Their research highlighted the importance of the binder material in achieving optimal strength and durability. In our study, Portland cement was the chosen binder, showcasing its effectiveness in binding ceramic tile aggregates and contributing to the overall structural integrity.13
It’s essential to note that variations in ceramic tile properties, such as size, type, and source, can impact concrete performance. Smith’s work emphasized the need for careful material selection, supporting our consideration of various tile types, including ceramic and porcelain, to ensure versatility and performance.6
Summary and conclusion
The study’s main goal is to replace both coarse and fine particles in concrete to create a material that is significantly more stable and long-lasting than ordinary concrete. A total of 90 specimens are manufactured and evaluated in terms of strength. Mix designs have been completed for all material replacements.
Conclusions
As tile aggregate replenishment increases, so does concrete’s workability. The inclusion of granite powder, which functions as an admixture because of its chemical makeup, increases the workability even further.
When ceramic aggregate was added to concrete, its characteristics increased linearly up to a 30% replacement, after which they dropped linearly.
According to the findings, the workability of the mixes is raised by 2.4%, 4.3%, 6.1%, 8.5%, 13.4%, 1.2%, 4.9%, 7.3%, 10.9%, 3.6%, 9.7%, 13.4%, and 15.8% and 64.5%, respectively, over the ordinary M25 concrete grade (M0).
In comparison to the other mixes, the concrete generated by the M3 mix exhibited superior “compressive strength, split tensile strength, and flexural strength”. However, mixtures containing up to 50% ceramic coarse aggregate may be applied.
When concrete is compared to ordinary concrete after 28 days of curing, the split tensile strength varies as follows: 1.95 percent, 5%, 7%, 1.18%, -1.6%, 0.39%, 1.9%, 3.1%, -2.3%, 0.78%, 3.5%, 3.9%, and 2.3%.
When comparing the strengths of all mixtures, M3, M8, and M12 have the greatest, with 30% coarse aggregate replacement. The inclusion of granite powder improves both strength and workability.
This achievement indicates a meticulous formulation that accelerates early strength for rapid construction phases while ensuring robust long-term performance, a critical innovation for efficient project timelines.
This demonstrates an innovative commitment to performance-driven standards, where the mix is designed not just to meet specifications but to excel in strength characteristics, ensuring reliability in structural applications.
Acknowledgement
The author would like to express their gratitude towards Tamilnadu College of Engineering, Coimbatore, Tamilnadu, India. For providing the necessary infrastructure to carry out this work successfully.
Conflicts of interest
No conflict of interest in this manuscript.
Author Contribution
Author SF is involved in data collection, experimental study and manuscript writing. Author LP and MS was involved in conceptualization, guidance and critical review of the manuscript.
Funding Sources
No funding source.
References
- Alsaffar, Abdul Kareem K., Saif S. Alquzweeni, Lubna R. Al-Ameer, Abduljabar H. Ali, Ahmed Mohamed, Humoud M. Aldaihani, A. Reham, “Development of Eco-Friendly Wall Insulation Layer Utilising the Wastes of the Packing Industry.” Heliyon 9 (11): 21799,2023
CrossRef - Al-Zboon, Kamel, Montasser Tahat, Ziad S. H. Abu-Hamatteh, and Mohammad S. Al-Harahsheh. “Recycling of Stone Cutting Sludge in Formulations of Bricks and Terrazzo Tiles.” Waste Management & Research: The Journal of the International Solid Wastes and Public Cleansing Association, ISWA 28 (6): 568–74,2010.
CrossRef - Chambers, J. M. Graphical Methods for Data Analysis. CRC Press,2018
CrossRef - Donatello, Shane, and Christopher R. Cheeseman. “Recycling and Recovery Routes for Incinerated Sewage Sludge Ash (ISSA): A Review.” Waste Management 33 (11): 2328–40,2013
CrossRef - Hurd, Wendy J., Melissa M. B. Morrow, Kenton R. Kaufman, and Kai-Nan An “Influence of Varying Level Terrain on Wheelchair Propulsion Biomechanics.” American Journal of Physical Medicine & Rehabilitation / Association of Academic Physiatrists 87 (12): 984–91,2008
CrossRef - Li, Zongjin,John Wiley & Sons Advanced Concrete Technology. 2011
CrossRef - Luhar, Ismail, Salmabanu Luhar, Mohd Mustafa Al Bakri Abdullah, Marcin Nabiałek, Andrei Victor Sandu, Janusz Szmidla, Anna Jurczyńska “Assessment of the Suitability of Ceramic Waste in Geopolymer Composites: An Appraisal.” Materials 14 (12). https://doi.org/10.3390/ma14123279,2021
CrossRef - Mangi, Sajjad Ali, Muhammad Saleem Raza, Shabir Hussain Khahro, Abdul Sami Qureshi, and Rabinder Kumar “Recycling of Ceramic Tiles Waste and Marble Waste in Sustainable Production of Concrete: A Review.” Environmental Science and Pollution Research International 29 (13): 18311–32.2022
CrossRef - Mhadhbi, Mohsen, Advanced Ceramic Materials. BoD – Books on Demand,2021.
CrossRef - Miccichè, Daniele, Maria Inès de Rosas, Massimo Vincenzo Ferro, Rosario Di Lorenzo, Stefano Puccio, and Antonino Pisciotta “Effects of Artificial Canopy Shading on Vegetative Growth and Ripening Processes of Cv. Nero d’Avola( L.).” Frontiers in Plant Science 14 (September): 1210574,2023.
CrossRef - Miličević, Ivana, Nina Štirmer, and Ivana Banjad Pečur, “Residual Mechanical Properties of Concrete Made with Crushed Clay Bricks and Roof Tiles Aggregate after Exposure to High Temperatures.” Materials 9 (4). https://doi.org/10.3390/ma9040295,2016.
CrossRef - Owen, Macaulay M., Emmanuel O. Achukwu, Ahmad Zafir Romli, Abdul Halim Bin Abdullah, Muhammad Hanif Ramlee, and Solehuddin Bin Shuib “Thermal and Mechanical Characterization of Composite Materials from Industrial Plastic Wastes and Recycled Nylon Fibers for Floor Paving Tiles Application.” Waste Management 166 (July): 25–34,2023
CrossRef - Pacheco-Torgal, Fernando, S. Jalali, João Labrincha, and V. M. John, Eco-Efficient Concrete. Elsevier,2013
CrossRef - Pacheco-Torgal, Fernando, Jamal Khatib, Francesco Colangelo, and Rabin Tuladhar,Use of Recycled Plastics in Eco-Efficient Concrete. Wood head Publishing,2008
- Siddique, Rafat ”Waste Materials and By-Products in Concrete”. Springer Science & Business Media,2007
- Sikalidis, Costas, Advances in Ceramics: Electric and Magnetic Ceramics, Bioceramics, Ceramics and Environment. BoD – Books on Demand,2011
CrossRef - Tiessler-Sala, Laura, Giuseppe Sciortino, Lur Alonso-Cotchico, Laura Masgrau, Agustí Lledós, and Jean-Didier Maréchal “Getting Deeper into the Molecular Events of Heme Binding Mechanisms: A Comparative Multi-Level Computational Study of HasAsm and HasAyp Hemophores.” Inorganic Chemistry 61 (43): 17068–79,2022.
CrossRef - T, Nelson Ponnu Durai, and Kandasamy S. “Investigation Study Data to Develop Sustainable Concrete Mix Using Waste Materials as Constituents.” Data in Brief 52 (February): 109837,2024
CrossRef

This work is licensed under a Creative Commons Attribution 4.0 International License.