Introduction
Calendering is one of the oldest techniques in polymer processing, used for fabricating high-volume plastic films or sheets 1,2. It is a simple two-step process involving the melting of the polymer and film formation by calendering rolls. Molten polymer passes through a set of rollers to create a uniform thickness and smooth surface. This process is crucial for polymer processing as it involves compressing and shaping the polymer material into a uniform thickness, enhancing its mechanical and surface properties. It ensures precise control over the thickness and dimensions of the final product, enabling the production of high-quality films, sheets, and other flat polymeric products used in various industries such as packaging, construction, automotive, textile, electrical, and medical sectors 2,3.
Poly(vinyl chloride) (PVC) is a widely used polymer in the calendering process 4–7. Due to the versatility, durability, and cost-effectiveness of PVC films, they are utilized in numerous industrial applications including packaging (shrink-wraps, cling films, blister packs), construction (wall coverings, flooring, window films, banners), automotive (interior trims, protective films), medical (intravenous bags, tubes), and electrical (insulative or protective films) 8. However, neat PVC cannot be melt-processed due to its low thermal degradation temperature (approximately 80°C) 9. Therefore, PVC must be mixed with suitable materials such as plasticizers 10, heat stabilizers 11, internal or external lubricants 12, and impact modifiers 13, to improve its processability and the final product properties.
Despite these enhancements, plasticizer migration in PVC films can lead to a decrease in mechanical properties and compromise the film’s long-term performance 14. Additionally, surface imperfections like air entrapment and defects during the calendering process can affect the visual appearance and functionality of the final product. Another significant drawback is the high energy consumption during polymer film processing by calendaring, even though it is cheaper than polymer casting route 7. Thus, new approaches to reduce polymer processing costs are of great importance, such as multi-layer calendering 15, innovative roller designs 16, new roll-heating routes 17, or process optimization using additives 18.
While organic and inorganic-based materials can be used as additives, low molecular weight and/or incompatible additives generally worsen the mechanical properties of the films. Miscible polymer blends present a promising solution for enhancing the aesthetic and mechanical properties of films while also reducing production costs in the calendering process. Further study is required to enable convenient polymer blending strategies to be used in practical calendering applications. The novelty of this study lies in exploring the potential of polymer blends to address these challenges effectively. By focusing on the blend of PVC with polymers like polymethyl methacrylate (PMMA) 19, polypropylene (PP) 20, and polyethylene (PE) 21, this research aims to offer innovative solutions that improve both mechanical properties and processing efficiency in the calendering process.
In this study, PVC/polymer blend films were prepared using the calendering process. Various amounts of PMMA, PP, and PE polymers were melt-mixed with plasticized PVC to obtain polymer blend films. Structural, morphological, thermal, and mechanical behavior of polymer blend films were characterized using various techniques. Additionally, the effects of miscibility on processing conditions were investigated. The results showed that polymer blending has significant potential in the calendering process of PVC films, offering improvements in both mechanical properties and processing efficiency.
Materials and Methods
Materials
CGCP, Thailand provided suspension-grade PVC with a K value of 65–67. In this work the composition of PVC compound was directly taken from an industrial available recipe from the production line. PP, PE, PMMA and reference PVC that consisted of PVC (100 phr), plasticizer (3 phr), CaCO3 (12.5 phr), TiO2 (7.5 phr), thermal stabilizer (2.75 phr), internal lubricant (1 phr), external lubricant (0.5 phr) and impact modifier (5 phr) were supplied by a local supplier.
Preparation of Polymer Blend Films
As given in Figure 1, polymer blend films were produced in three steps. In the first step, the reference PVC compound was prepared by using a hot/cold mixer (Dersan, DM-LB10) at ⁓110⁰C, 750 rpm for ⁓8 min and ⁓45⁰C, 250 rpm for ⁓3 min, respectively. In the second step, blending of PVC with PE, PP and PMMA was performed at different ratios (wt.%) by using a laboratory scale blender (Entex, L-WE30) at ⁓165⁰C and 100 rpm for ⁓30 min. In the final step, PVC compound and PVC/polymer blends were calendered by using lab-scale calendering machine with two rollers. During calendering process, banking times and electrical current values were also measured. PVC blend compositions and their properties were given in Table 1. In addition to compositional information, Table 1 gives electrical current values during the process. It is obvious from the results, all blends resulted in lower current values that is an indication of lower energy consumption and decrease in processing costs. Furthermore, banking times were decreased in the range of 2.5 – 12% depending on blend composition. So, blending PVC with other polymers can improve production speeds and synergistically decrease processing cost. It should be noted that 90PVC/10PP and 90PVC/10PE blend films could not be fabricated by calendering.
Characterization of Polymer Blend Films
The structural behavior of polymer blend films was characterized by using attenuated total internal reflectance (ATR) mode (Perkin Elmer, Spectrum-2 IR spectrometer) of a Fourier transform infra-red spectroscopy (FTIR) system. Between 450 and 4000 cm−1, spectra were captured in the transmittance mode at a scan rate of 4 scans, with a spectral resolution of 4 cm−1.
The thermal behavior of polymer blend films was examined by differential scanning calorimetry (DSC, Seiko). Under N2 atmosphere, one cooling and two heating scans were conducted between -70°C and 180°C, at 5°C min-1 cooling/heating rate, with an amplitude of 1°C, and a time of 60 s. The total run time per sample was ⁓2 h and the sample weighed ~7-8 mg. The glass transition (Tg) temperature was calculated from the reversing heat flow curves using the second heating scan in order to produce a comparable thermal history.
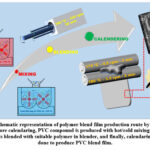 |
Figure 1: Schematic representation of polymer blend film production route by calendering process. Before calendaring, PVC compound is produced with hot/cold mixing.
Click here to View Figure
|
To characterize the morphology of polymer blend films, JEOL JSM-6400, 30kV field emission scanning electron microscopy (FESEM) was utilized. A blade was employed to cut the polymer mix films, and Au/Pd alloy was sputter coated onto the cross-section of the sample prior to analysis with a coating thickness in the range of 3 – 6 nm.
Utilizing universal testing equipment (Devotrans, DVT GPU/RD), the mechanical properties of polymer blend films, such as elastic modulus, yield point, their tensile strength and tensile strain, were assessed. A blade was used to cut the samples with certain dimensions (50 mm x 5 mm). A thickness meter (Asimeto) was used to determine the average thickness of the composites before the mechanical test. For every sample, three mechanical tests were made at a speed of 1.5 cm min-1.
Table 1: PVC blend compositions and their properties
Sample ID#
|
Polymer Blends
|
Ratio (wt%)
|
Film Formation
|
Surface Properties
|
Current Values During Calendering (A)
|
Banking Time (s)
|
PVC
|
PVC
|
100
|
√ |
Smooth
|
37
|
85
|
99PVC/1PP
|
PVC/PP
|
99/1
|
√ |
Rough
|
32 (-13.5%↓)
|
83 (-2.35%↓)
|
95PVC/5PP
|
PVC/PP
|
95/5
|
√ |
Rough
|
28 (-24.3%↓)
|
77 (-9.41%↓)
|
90PVC/10PP
|
PVC/PP
|
90/10
|
x |
x |
x |
x |
99PVC/1PE
|
PVC/PE
|
99/1
|
√ |
Rough
|
30 (-18.9%↓)
|
78 (-8.24%↓)
|
95PVC/5PE
|
PVC/PE
|
95/5
|
√ |
Rough
|
25 (-32.4%↓)
|
75 (-11.76%↓)
|
90PVC/10PE
|
PVC/PE
|
90/10
|
x |
x |
x |
x |
99PVC/1PMMA
|
PVC/PMMA
|
99/1
|
√ |
Smooth
|
34 (-8.1%↓)
|
82 (-3.53%↓)
|
95PVC/5PMMA
|
PVC/PMMA
|
95/5
|
√ |
Smooth
|
30 (-18.9%↓)
|
80 (-5.88%↓)
|
90PVC/10PMMA
|
PVC/PMMA
|
90/10
|
√ |
Smooth
|
32 (-13.5%↓)
|
81 (-4.71%↓)
|
Results and Discussion
Structural Analysis
FTIR spectroscopy was carried out to analyze the structural behavior of PVC polymer blend films. FTIR spectra were recorded in transmittance mode in between 4000 – 450 cm-1 region and given in Figure 2. The chemical structures of polymers used in composite films were also shown in Figure 2 a-c. The characteristic peaks belonging to IR spectrum of PVC, PMMA, PE and PP can also be seen from Table 2. The characteristic peaks of plasticized PVC films can be seen in Fig.2. The peaks at 2851, 2922, and 2958 cm-1 were assigned to -CH stretching vibrations. CH2-Cl angular deformation vibration at 1425 cm-1, CH-Cl out of plane angular deformation vibration at 1244 cm-1 and C-Cl bond stretching vibrations at 874 cm-1 were observed for all samples. The peaks at 964 and 608 cm-1 represented trans C-H wagging, and cis C-H wagging vibrations, respectively. The peaks at 1735 and 1330 cm-1 were related to -C=O stretching vibrations of carbonyl group of plasticizer and deformation vibrations of -CH2 22–24.
For PVC/PE films, when PE content in the blend increased to 5%, the peaks at 2851 and 2922 cm-1 become more distinct, these peaks were assigned to symmetrical and asymmetrical C-H stretching vibrations of PE, respectively. Also, CH2-rocking and scissoring vibration peaks at 711 and 1459 cm-1 could be seen at Fig. 2a 25. For PVC/PP blend films, the peaks at 1450, 2851, 2918 cm-1 were assigned to -CH2– symmetrical bending, -CH2– symmetrical stretching and -CH2– asymmetrical stretching, respectively 26. Also, symmetrical bending vibration of -CH3 group was detected at 1376 cm-1 (Fig.2b) 27.
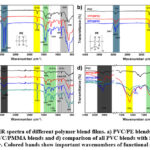 |
Figure 2: FTIR spectra of different polymer blend films. a) PVC/PE blends, b) PVC/PP blends, c) PVC/PMMA blends and d) comparison of all PVC blends with 5% additive polymer.
Click here to View Figure
|
For PVC/PMMA blend films, the peaks at 2918 and 1731 cm−1 represented stretching vibrations of C-H, and C=O groups, respectively (Fig.2c). The peaks at 875, 1192, 1427, 1731, and 2949 cm−1 were related to stretching vibrations of C-Cl, -O-CH3, CH3, C=O, and C-H groups in the polymer blends, respectively. In parallel with the literature, the characteristic peaks of plasticized PVC 1735, 1244, 670 cm-1 were shifted to 1731, 1247 and 682 cm-1 in PVC/PMMA polymer blend films 23,28–30. Also, intensities of the carbonyl peaks were increased with the increment of PMMA amount in PVC/PMMA polymer blends. As previously described by Soman and Kelkar, miscibility might be enhanced by a particular hydrogen bonding interaction between the carbonyl group (C=O) of PMMA and the hydrogen from (-HC-Cl) of PVC 22.
Table 2: Vibational modes observed in different polymer blends
Vibrational Modes
|
Wavenumber (cm-1)
|
PVC
|
95PVC/5PMMA
|
95PVC/5PP
|
95PVC/5PE
|
C-H stretching
|
2851, 2922, 2958
|
2850, 2918, 2949
|
2851, 2918, 2958
|
2851, 2922, 2958
|
C=O stretching
|
1735
|
1731
|
1734
|
1735
|
CH2 deformation
|
1425, 1459
|
1427
|
1425,1450
|
1425,1459
|
-CH3 bending
|
|
|
1376
|
|
CH2 bending
|
1330
|
1330
|
1330
|
1330
|
CH-Cl rocking
|
1244
|
1247
|
1253
|
1253
|
-OCH3 stretching
|
|
1192, 1150
|
|
|
-CH3 rocking
|
|
|
1167, 968
|
|
trans CH wagging
|
964
|
964
|
964
|
964
|
C-Cl stretching
|
874, 670
|
875, 682
|
874, 678
|
874, 670
|
-CH2 rocking
|
|
|
844 – 810
|
731, 711
|
cis CH wagging
|
608
|
609
|
611
|
608
|
Thermal Analysis
The thermal behavior of PVC, 5PE/95PVC, 5PP/95PVC and 5PMMA/95PVC blend films as a function of temperature is presented in Fig. 3. To make it easier to compare the transitions of the various samples, curves in the figure were intentionally moved vertically along the heat flow axis (Figure 3). The discussion was based on the second heating of every sample because the first heating and cooling was done to create a similar thermal history to all samples.
Commercial PVC is an amorphous polymer and only glass transition temperature (Tg), can be observed which can be around 70-90°C depending on the composition of PVC for film making. While neat PVC shows a a Tg of 90°C, this value decreases with the addition of plasticizer. PVC, 5PP/95PVC and 5PE/95PVC film samples showed a Tg of 72.3°C, this shows that PP or PE have no effect on Tg of PVC. It can be clearly seen that Tg value increased from 72.3°C to 75.6°C with the addition of PMMA into PVC composition (Fig. 3 inset). This is parallel with the literature 31. Change in the glass transition is the obvious proof the miscibility and it also shows that PVC/PMMA polymer blends are compatible to each other 30. From Fig. 3, it can also be seen cold crystallization exotherm both 5PP/95PVC and 5PE/95PVC film samples. The cold crystallization temperatures (Tcc) were measured as 141.02°C and 129.35°C from the maximum value of cold crystallization for 5PP/95PVC and 5PE/95PVC film samples, respectively.
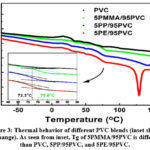 |
Figure 3: Thermal behavior of different PVC blends (inset shows Tg change). As seen from inset, Tg of 5PMMA/95PVC is different than PVC, 5PP/95PVC, and 5PE/95PVC.
Click here to View Figure
|
Morphological Analysis
The morphology of blends is evaluated by some aspects such as scale, geometry, and spatial distribution of phase separation and so on. It is directly influenced by the type of polymers and ratio of the components. Polymer blends can be classified as miscible blends and immiscible blends due to separation of the phases. While miscible blends behave as one single phase, immiscible blends tend to exhibit continuous and dispersed phases and dispersed phase is generally observed as spherical, particle, plate or channel-like geometry in the continuous phase especially at low concentrations. In our case, PVC, 95PVC/5PP, 95PVC/5PE, 95PVC/5PMMA were chosen for morphology analysis. To analyze the phase morphology and phase interphase, FESEM images were given at different magnifications such as 5k, 20k and 50kx. While low magnification images were given to observe the continuous and dispersed phases, high magnification images are useful to observe the size, geometry and interphase of the phases. Fig. 4a is the cross-sectional image of PVC film. PVC has been successfully melted. As previously mentioned, an industrial recipe was used for preparation of PVC compound and the particles throughout the film cross-section were probably inorganic materials such as CaCO3 and TiO2. These particles were also observed for all blends. 95PVC/5PP based blend film can be seen from Fig. 4b. PVC was the continuous phase and PP phase was not found to be miscible in PVC matrix. PP phase was indicated by arrows in SEM images. The morphology of PP phase was almost like stretched plates and stretched channels. 95PVC/5PE based blend film can be seen from Fig. 4c. PVC was the continuous phase and PE phase was not found to be miscible in PVC matrix that was also reported in previous studies 32. As shown by the arrows in FESEM images, the morphology of PP phase was almost like elliptical particles. 95PVC/5PE based blend film was shown Fig. 4d. Unlike PP and PE blends PMMA was found to show higher miscibility in PVC. As previously mentioned in FTIR analysis, the miscibility of PMMA in PVC was reported to be caused by interaction between -CHCl and C=O groups of PVC of PMMA, respectively 30.
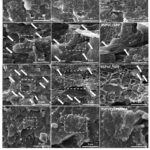 |
Figure 4: SEM images of different polymer blend films @ 5kx, 20kx and 50kx a) PVC film, b) 95PVC/5PE blend film, c) 95PVC/5PP blend film, and d) 95PVC/5PMMA blend film.
Click here to View Figure
|
Mechanical Characterization
Stress-strain curves of PVC, PVC/PE, PVC/PP and PVC/PMMA blend films can be seen from Fig. 5. Yield stress, strain at break, elastic modulus values of the samples and rational changes compared to PVC were summarized in Table 3. Since 90PVC/10PP and 90PVC/10PE blend films could not be fabricated by calendering, their mechanical testing was not performed. PVC showed classical response with the yield strength, strain at break and elastic modulus values of 70.36 MPa, 13.18 % and 660 MPa respectively. PVC/PP composites showed increase in yield stress and elastic modulus as PVC<95PVC/5PP<99PVC/1PP. On the other hand, due to higher modulus, strain values at break showed drop as 95PVC/5PP<99PVC/1PP<PVC. PVC/PE blend showed slight increase in mechanical performance for 99PVC/1PE and decrease for 95PVC/5PE. That can be given as 95PVC/5PE<PVC<99PVC/1PE and assumed to be caused by immiscibility of PE in PVC. PVC/PE blends showed relatively lower mechanical performance compared to PVC/PP samples as given in Table 3. That can be explained by FESEM images. As can be seen from low and high magnification images PE showed higher phase separation. By incorporation of PMMA into PVC, both yield stress and elastic modulus increased as PVC<99PVC/1PE<95PVC/5PE and strain at break decreased due to higher elastic modulus and rigid structure of PMMA. Fig. 5d shows the performance of PVC and blend films. As obvious from the graph, PMMA blends showed the highest performance and mechanical performance of the samples can be given as PVC/PE<PVC<PVC/PE<PVC/PMMA. That is also parallel with morphological analysis. As mentioned previously, PMMA was miscible in PVC due to interactions between two polymers.
Table 3: PVC blend compositions and their properties
Sample ID#
|
Yield Stress (MPa)
|
Strain at Break (%)
|
Elastic Modulus (MPa)
|
PVC
|
70.36
|
13.18
|
660
|
99PVC/1PP
|
81.64 (16%↑)
|
8.20 (-37.8%↓)
|
740 (12.1%↑)
|
95PVC/5PP
|
79.47 (13.9%↑)
|
7.85 (-40.4%↓)
|
742 (12.4%↑)
|
99PVC/1PE
|
73.79 (4.9%↑)
|
12.77 (-3.1%↓)
|
695 (5.3%↑)
|
95PVC/5PE
|
68.94 (-2.0%↓)
|
13.44 (1.9%↑)
|
654 (-0.9%↓)
|
99PVC/1PMMA
|
87.62 (24.5%↑)
|
12.55 (-4.8%↓)
|
819 (24.0%↑)
|
95PVC/5PMMA
|
91.26 (29.7%↑)
|
8.54 (-35.2%↓)
|
850 (28.8%↑)
|
90PVC/10PMMA
|
96.26 (36.8%↑)
|
8.67 (-34.2%↓)
|
890 (34.8%↑)
|
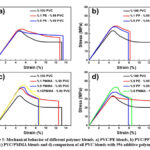 |
Figure 5: Mechanical behavior of different polymer blends. a) PVC/PE blends, b) PVC/PP blends, c) PVC/PMMA blends and d) comparison of all PVC blends with 5% additive polymer
Click here to View Figure
|
Conclusions
In this study, PVC/PE, PVC/PP, and PVC/PMMA blend films were prepared using a straightforward 3-step process (melt mixing, blending, calendering). The aim was to examine the impact of blending on calendering conditions and film properties. The characterization of structural, morphological, thermal, and mechanical behavior revealed that while PVC/PE and PVC/PP blends were immiscible, PVC/PMMA blends were consistently miscible, irrespective of the PMMA ratio. This miscibility significantly enhanced the mechanical properties, with yield stress and elastic modulus of 95PVC/5PMMA blend films increasing by 29.7% and 28.8%, respectively, compared to pure PVC films. Additionally, blending with PMMA reduced energy consumption and processing costs. These findings underscore the significant potential of PVC/PMMA blends in improving the efficiency and effectiveness of the calendering process for PVC films.
Acknowledgement
The authors wish to thank Elif DEMIR for DSC measurements.
Conflict of Interest
There is no conflict of interest.
Funding Source
This project was funded by Yalova University, BAP (Scientific Research Project) Project No: 2022/YL/0002.
References
- Mitsoulis E,Polychronopoulos ND,Hatzikiriakos SG. Calendering of Thermoplastics: Models and Computations. International Polymer Processing 2022; 37 (4): 341–356. doi:10.1515/ipp-2021-4214,
CrossRef
- Gedde UW, Hedenqvist MS, Hakkarainen M, Nilsson F, Das O. Processing of Polymeric Materials. In Applied Polymer Science; Gedde, U. W., Hedenqvist, M. S., Hakkarainen, M., Nilsson, F., Das, O., Eds.; Springer International Publishing: Cham, 2021; 453–487. doi:10.1007/978-3-030-68472-3_8,
CrossRef
- Gaskell RE. The Calendering of Plastic Materials. J Appl Mech 1950; 17 (3): 334–336. doi:10.1115/1.4010136,
CrossRef
- Titow WV. Calendering of PVC. In PVC Technology; Titow, W. V, Ed.; Springer Netherlands: Dordrecht, 1984; pp 803–848. doi:10.1007/978-94-009-5614-8_18,
CrossRef
- Bourgeois JL, Agassant JF. Calendering of PVC: Defects in Calendered PVC Films and Sheets. Journal of Macromolecular Science, Part B 1977; 14 (3): 367–385. doi:10.1080/00222347708212907,
CrossRef
- Ray A, Shenoy AV. PVC Calendering: A Simplified Prediction Technique. J Appl Polym Sci 1985; 30 (1): 1–18. doi:10.1002/app.1985.070300101,
CrossRef
- Gavim AEX,Mascarenhas R de O,Sbrissia LS,Júnior JVB,Casagrande TR,Macedo AG. Identifying the Manufacturing Process of PVC Films by Nondestructive Morphological Analyses. Mater Lett 2023; 338: 134065. doi:10.1016/j.matlet.2023.134065,
CrossRef
- Grosu E. Applications of Polyvinylchloride (PVC)/Thermoplastic Nano-, Micro- and Macroblends. In Polyvinylchloride-based Blends; Darie-Nita, R. N., Ed.; Springer, 2022; 75–89. doi:10.1007/978-3-030-78455-3_4,
CrossRef
- McNeill IC, Memetea L, Cole WJ. A Study of the Products of PVC Thermal Degradation. Polym Degrad Stab 1995; 49 (1): 181–191. doi:10.1016/0141-3910(95)00064-S,
CrossRef
- Menges G,Berndtsen N. Polyvinyl Chloride – Processing and Structure. Pure and Applied Chemistry 1977; 49 (5): 597–613. doi:10.1351/pac197749050597,
CrossRef
- Jamarani R, Halloran MW, Panchal K, Garcia-Valdez O, Mafi R, Nicell JA, Leask RL, Marić M. Additives to Prevent the Formation of Surface Defects during Poly(Vinyl Chloride) Calendering. Polym Eng Sci 2021; 61 (4): 1209–1219. doi:10.1002/pen.25667,
CrossRef
- Vlachopoulos J, Hrymak AN. Calendering Poly(Vinyl Chloride): Theory and Experiments. Polym Eng Sci 1980; 20 (11): 725–731. doi:10.1002/pen.760201105,
CrossRef
- Jazi SHS, Esfahany MN, Bagheri R. Investigation of the Addition of Nano-CaCo3 at Dry Mixing or Onset of Fusion on the Dispersion, Torque, and Mechanical Properties of Compounded PVC. Journal of Vinyl and Additive Technology 2012; 18 (3): 153–160. doi:10.1002/vnl.20317,
CrossRef
- Till DE, Reid RC, Schwartz PS, Sidman KR, Valentine JR, Whelan RH. Plasticizer Migration from Polyvinyl Chloride Film to Solvents and Foods. Food and Chemical Toxicology 1982; 20 (1): 95–104. doi:10.1016/S0278-6915(82)80016-1,
CrossRef
- Shin J, Park JH, Kim J, Yoon KJ, Son J-W, Lee J-H, Lee H-W, Ji H-I. Suppression of Processing Defects in Large-Scale Anode of Planar Solid Oxide Fuel Cell via Multi-Layer Roll Calendering. J Alloys Compd 2020; 812: 152113. doi:10.1016/j.jallcom.2019.152113,
CrossRef
- Tseng AA, Sun PF. A Finite Difference Study of Roll Design in Calendering Processing. International Polymer Processing 1990; 5 (4): 292–299. doi:10.3139/217.900292,
CrossRef
- Gupta N, Kanth N. Study of Heat Conduction inside Rolling Calender Nip for Different Roll Temperatures. J Phys Conf Ser 2019; 1276 (1): 12044. doi:10.1088/1742-6596/1276/1/012044,
CrossRef
- Rideout A, Panchal K, Maric M, Leask R, Nicell J. Prevention of Surface Defects in Calendered Poly(Vinyl Chloride) Sheets Using a Succinate‐capped Poly(Caprolactone) Additive. Journal of Vinyl and Additive Technology 2024; 30 (3): 814–824. doi:10.1002/vnl.22087,
CrossRef
- Omidvar A, Masoumi S, Monsefi M, Jafarzadeh Y, Nasiri M, Hazrati H. PVC/PMMA Blend Ultrafiltration Membranes for Oil-in-Water Emulsion Separation. Polymer Bulletin 2023; 80 (8): 9275–9295. doi:10.1007/s00289-022-04514-6,
CrossRef
- Flores-Guía TE, Caldera-Villalobos M, Cabrera-Munguía DA, Cano-Salazar LF, Claudio-Rizo JA. 6 – Poly(Vinyl Chloride)/Vinyl Plastic Blends, Interpenetrating Polymeric Networks, and Gels. In Poly(vinyl chloride)-based Blends, Interpenetrating Polymer Networks (IPNs), and Gels; Thomas, S., Akhina, H., Eds.; Elsevier, 2024; 155–177. doi:https://doi.org/10.1016/B978-0-323-99474-3.00001-X,
CrossRef
- Khakberdiev EO, Maou S, Berdinazarov QN, Ibragimov JK, Ashurov NR. Unveiling the Morphological Features of PVC/PE Polymer Blends: Insights into Improved Performance. Egypt J Chem 2024; 67 (4): 87–92. doi:10.21608/ejchem.2023.225230.8311,
CrossRef
- Soman V V, Kelkar DS. FTIR Studies of Doped PMMA – PVC Blend System. Macromol Symp 2009; 277 (1): 152–161. doi:10.1002/masy.200950319,
CrossRef
- Chen J, Nie XA, Jiang JC, Zhou YH. Thermal Degradation and Plasticizing Mechanism of Poly(Vinyl Chloride) Plasticized with a Novel Cardanol Derived Plasticizer. IOP Conf Ser Mater Sci Eng 2018; 292 (1): 012008. doi:10.1088/1757-899X/292/1/012008,
CrossRef
- Tan J, Liu B, Fu Q, Wang L, Xin J, Zhu X. Role of the Oxethyl Unit in the Structure of Vegetable Oil-Based Plasticizer for PVC: An Efficient Strategy to Enhance Compatibility and Plasticization. Polymers. 2019. doi:10.3390/polym11050779,
CrossRef
- Gulmine J V, Janissek PR, Heise HM, Akcelrud L. Polyethylene Characterization by FTIR. Polym Test 2002; 21 (5): 557–563. doi:10.1016/S0142-9418(01)00124-6,
CrossRef
- Gopanna A, Mandapati RN, Thomas SP, Rajan K, Chavali M. Fourier Transform Infrared Spectroscopy (FTIR), Raman Spectroscopy and Wide-Angle X-Ray Scattering (WAXS) of Polypropylene (PP)/Cyclic Olefin Copolymer (COC) Blends for Qualitative and Quantitative Analysis. Polymer Bulletin 2019; 76 (8): 4259–4274. doi:10.1007/s00289-018-2599-0,
CrossRef
- Sakai K, Sobue H. Study of Structure and Thermal Properties of Polypropylene and Chlorinated Polypropylene by Infrared Spectroscopy and Differential Scanning Calorimetry. J Appl Polym Sci 1972; 16 (10): 2657–2670. doi:10.1002/app.1972.070161018,
CrossRef
- Ramesh S, Leen KH, Kumutha K, Arof AK. FTIR Studies of PVC/PMMA Blend Based Polymer Electrolytes. Spectrochim Acta A Mol Biomol Spectrosc 2007; 66 (4): 1237–1242. doi:10.1016/j.saa.2006.06.012,
CrossRef
- Fekete E, Földes E, Pukánszky B. Effect of Molecular Interactions on the Miscibility and Structure of Polymer Blends. Eur Polym J 2005; 41 (4): 727–736. doi:10.1016/j.eurpolymj.2004.10.038,
CrossRef
- Aouachria K, Belhaneche-Bensemra N. Miscibility of PVC/PMMA Blends by Vicat Softening Temperature, Viscometry, DSC and FTIR Analysis. Polym Test 2006; 25 (8): 1101–1108. doi:https://doi.org/10.1016/j.polymertesting.2006.07.007,
CrossRef
- Karlou K, Schneider HA. DSC and P-V-T Study of PVC/PMMA Blends. J Therm Anal Calorim 2000; 59 (1): 59–69. doi:10.1023/A:1010119525345,
CrossRef
- Thongpin C, Santavitee O, Sombatsompop N. Degradation Mechanism and Mechanical Properties of PVC in PVC-PE Melt Blends: Effects of Molecular Architecture, Content, and MFI of PE. Journal of Vinyl & Additive Technology 2006; 12 (3): 115–123, doi:10.1002/vnl.20079.
CrossRef

This work is licensed under a Creative Commons Attribution 4.0 International License.